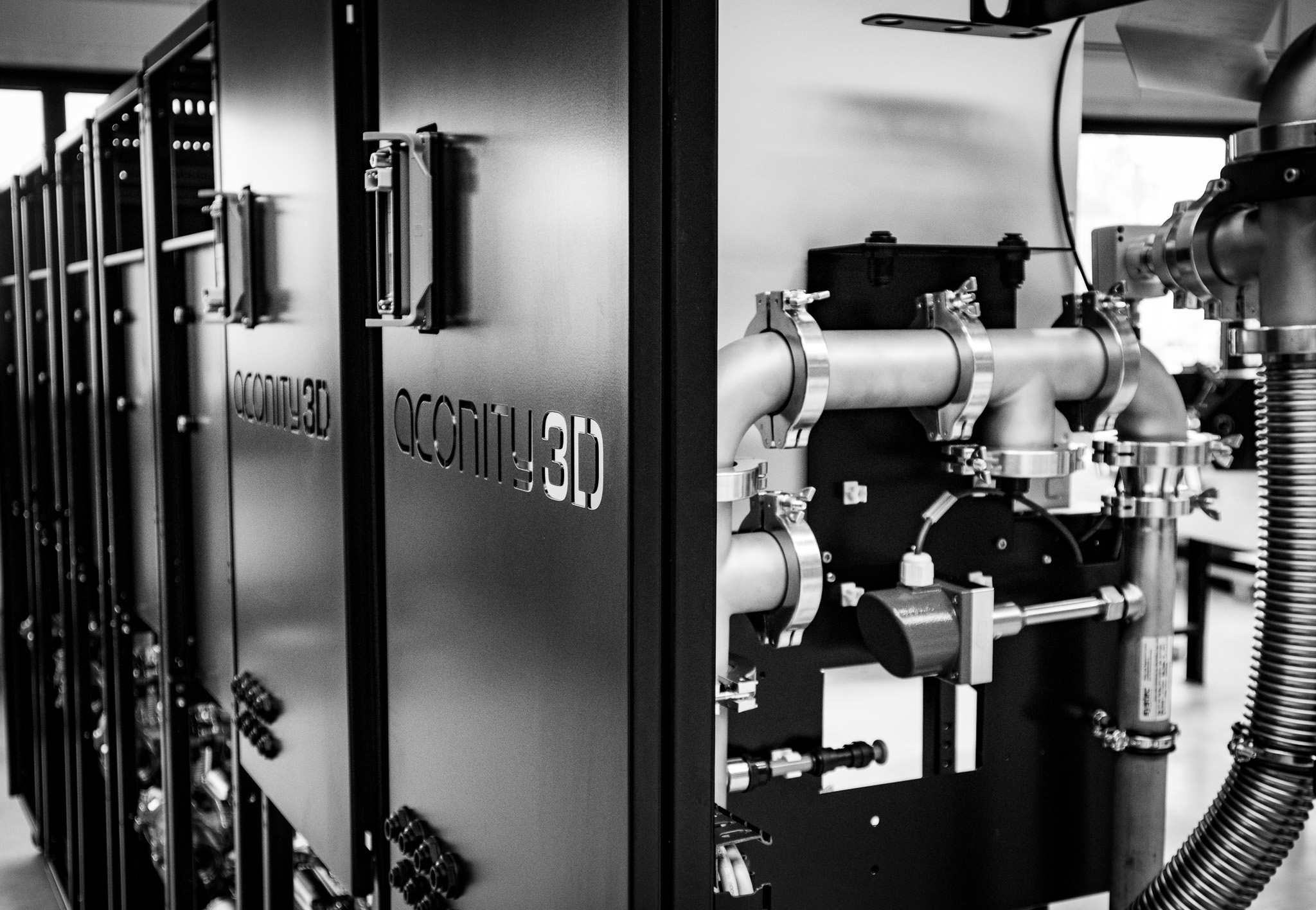
Series Production of the Aconityππππππππππππ Has Started
Modular filtration redefined for industrial metal AM applications
Aconity3D is proud to announce the start of series production for the Aconityππππππππππππ – a next-generation filtration system setting new standards in reliability, safety, and operational efficiency for metal additive manufacturing environments.
Designed as a fully modular and scalable solution, the Aconityππππππππππππ combines robust mechanical design with intelligent system integration to ensure long-term, uninterrupted machine uptime.
Reliable by Design
- – Advanced internal monitoring and diagnostic capabilities*
- – Redesigned chalk conveyance system
- – Completely enclosed, dust-tight housing
- – Proven long-term stability, even during continuous week-long build jobs
- – Rugged construction for industrial-grade operation
Low Maintenance β High Efficiency
- – Long-life sintered filter elements with a typical service life of 2 to 5 years
- – Enlarged chalk reservoir for extended operation
- – No machine downtime required for routine filter changes
Enhanced Safety for AM Operations
- – Fully encapsulated extraction chamber
- – Dust-to-bucket handling minimizes manual intervention
- – In development: controlled oxidation for direct passivation of reactive materials
- – Significant reduction of fire and explosion risks in powder-rich environments
Effective immediately, the Aconityππππππππππππ is a standard component in all Aconityπ systems and is also available as a retrofit option for existing machines.
We continue to deliver forward-looking solutions that address the practical needs of industrial AM usersβensuring safer, more reliable, and more efficient production environments.
For further information or individual inquiries, please contact our sales team.