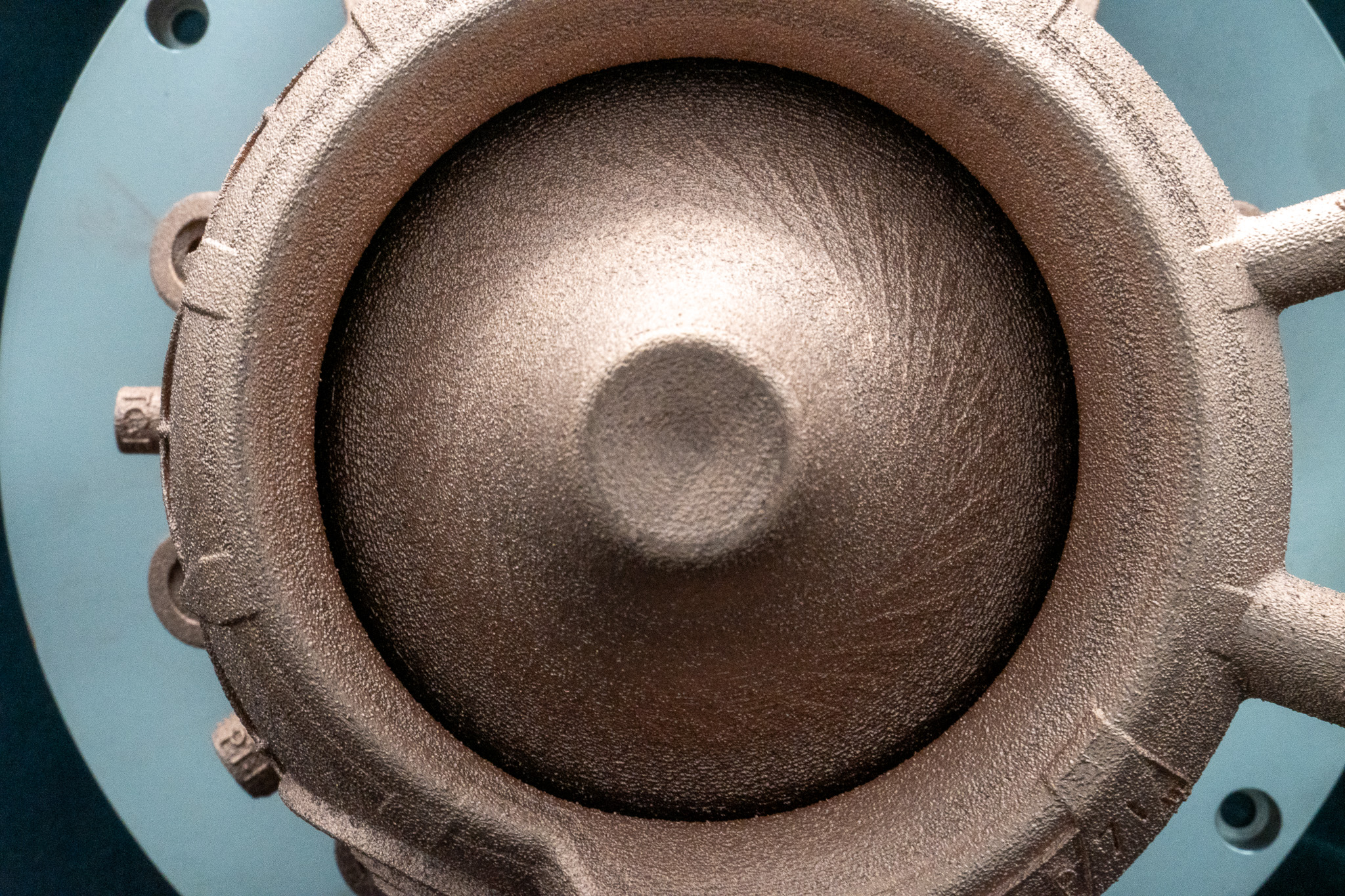
Aconity3D 3D Prints AI-Designed Aerospike Rocket Engine in Advanced Copper Alloy
Groundbreaking milestone: Hot-fire success on first attempt for fully AI-generated rocket engine, produced as a monolithic copper part
Aconity3D, in collaboration with leading partners from research and industry, has successfully manufactured and tested a cryogenic aerospike rocket engine – entirely designed by artificial intelligence and 3D-printed in a single monolithic part using a high-performance aerospace copper alloy (CuCrZr).
The engine was printed using our AconityMIDI+, a machine designed for efficient industrial LPBF applications – using the IPG YLR 3000/1000 AM laser system. Subsequent depowdering was carried out by Solukon and heat treatment by the Fraunhofer Institute for Laser Technology (ILT). The Race 2 Space Team from the University of Sheffield prepared the engine for the test campaign and provided expert support throughout.
The outcome: A successful hot-fire test on the first attempt.
LEAP 71 and the Role of AI in Engineering Design
The true innovation behind this achievement lies in the design process itself. The engine was created entirely by Noyron, a large-scale computational engineering model developed by LEAP 71. Unlike traditional engineering workflows, which require iterative, human-led processes – Noyron autonomously generated a 5 kN Kerolox aerospike rocket engine design in a matter of minutes.
LEAP 71’s approach redefines engineering by combining physics, geometry, and performance constraints into executable code, allowing AI to explore design spaces beyond human intuition. This is not AI assisting engineers – it is AI acting as the engineer, capable of producing hardware-ready geometries without manual intervention.
Aerospike engines are among the most challenging propulsion systems in aerospace. Their “inside-out” design ensures high efficiency across all altitudes, eliminating the need for heavy nozzle extensions typical of vacuum-optimized engines. Yet this same geometry makes them incredibly difficult to design and cool – until now.
A Technical Showcase in Additive Manufacturing
The printed engine features a highly intricate internal network of regenerative cooling channels, through which both liquid oxygen (LOX) and kerosene flow. These channels prevent the combustion chamber from overheating. The hot kerosene is then mixed with gaseous oxygen and ignited to generate thrust.
Manufacturing such a geometry as a single monolithic component in CuCrZr, with internal flow paths and thermal loads in mind, showcases the capabilities of Aconity3D’s advanced AM systems and the readiness of AI-generated designs for real-world use.
Looking Ahead: Scaling to 20 kN with Methane and LOX
Following the successful 5 kN test, development is already underway for the next step: a 20 kN aerospike thruster running on methane and liquid oxygen. This marks a new era in propulsion development – one where artificial intelligence and metal additive manufacturing enable faster, more efficient, and radically innovative hardware.